确保连接技术的可持续性
纵观全球汽车行业的发展,我们发现,近年来欧洲新乘用车和轻型商用车的重量在不断上升,从2000年的约1,268公斤增长到2010年的1,360公斤,再到2020年的约1,420公斤。随着越来越多混合动力汽车和电动汽车的出现,这一趋势可能会进一步加剧,因为仅电池重量一项,电动汽车就比传统发动机汽车平均重300公斤。
www.arnold-fastening.com
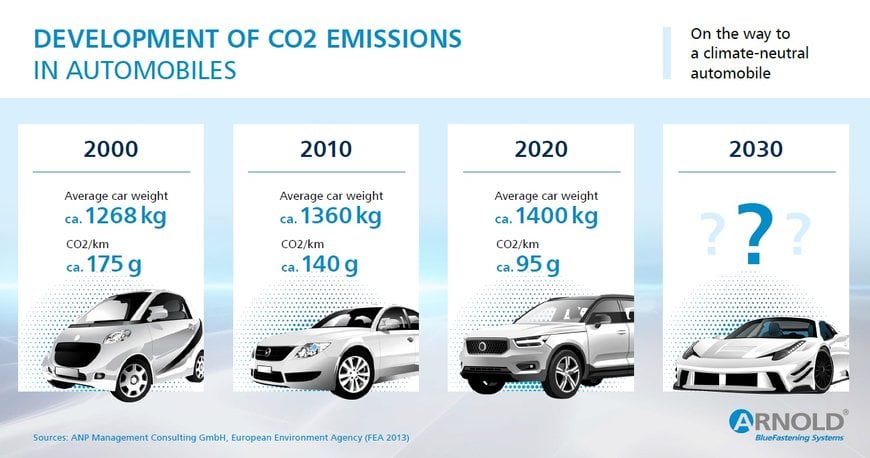
得益于燃料消耗的优化和创新的新型动力总成设计,二氧化碳排放量已大幅减少,从2000年的每公里排放约175克二氧化碳降至2010年的140克,并在2020年进一步减少到95克。如果要在未来几年实现气候保护目标,这一趋势必须持续下去。
在此背景下,可持续发展问题成为德国阿诺德集团的首要任务。除了电动出行、国际化、轻量化工程和数字化之外,可持续发展也是其五大战略方向之一。
该公司专家意识到,每个产品在其整个价值链中都会产生独特的碳足迹,而且所有供应链成员的排放量都会被累计。这意味着,处于供应链下游的公司在采购产品和服务的时候会承接上游供应商的排放量,然后将其自身排放量转嫁给客户。
ACO2-Save提供多种减少二氧化碳排放的方法
在此背景下,阿诺德公司发起了ACO2-Save计划(此处的“A”代表Arnold阿诺德)。该计划通过可持续方式设计和应用紧固件和冷成形件来积极支持客户减少二氧化碳排放。在产品开发过程中,阿诺德就已经进行了相应的二氧化碳计算。当客户要求阿诺德制造某个零件时,公司会使用专门开发的二氧化碳计算器确定产品的碳足迹,然后共同进行优化。这样做的目的是在开发完成后能获得技术质量高且成本和二氧化碳排放量都经过优化的产品。
其设计过程包括以下步骤:通过数字预测工具进行二氧化碳优化工程设计,通过改变生产技术或连接技术对二氧化碳进行优化分析,并使用创新的连接元件或系统。
ACO2 Save的成功案例:一种特殊的铝制螺钉,体积为8,733立方毫米,单件重量为23.58克,之前通过传统机械加工生产,坯料体积为25,630立方毫米,每件重量为69.2克。经过ACO² Save分析后,该零件改为Conform Next产品系列中的成型零件。结果优化后,成型坯料的体积仅为9,135立方毫米,单件重量为24.82克。除了在冷成型过程中减少材料投入,显著优化成本外,它还对特殊螺杆的产品碳足迹产生了重大影响。
通过ACO2-Save及相关生产技术的改进,德国的能源效率有所提升,螺钉生产过程中产生的二氧化碳排放量也减少了45%。