www.engineering-china.com
23
'22
Written on Modified on
确保连接技术的可持续性
放眼全球汽车行业的发展,可以看到近年来欧洲新的乘用车和轻型商用车的重量从 2000 年的 1268 公斤左右增至 2010 年的 1360 公斤,2020 年达到 1420 公斤左右。更多的混合动力和电动汽车这一趋势可能会加剧这一发展,因为电池的重量让电动汽车的平均重量比配备传统发动机的汽车要重 300 公斤。
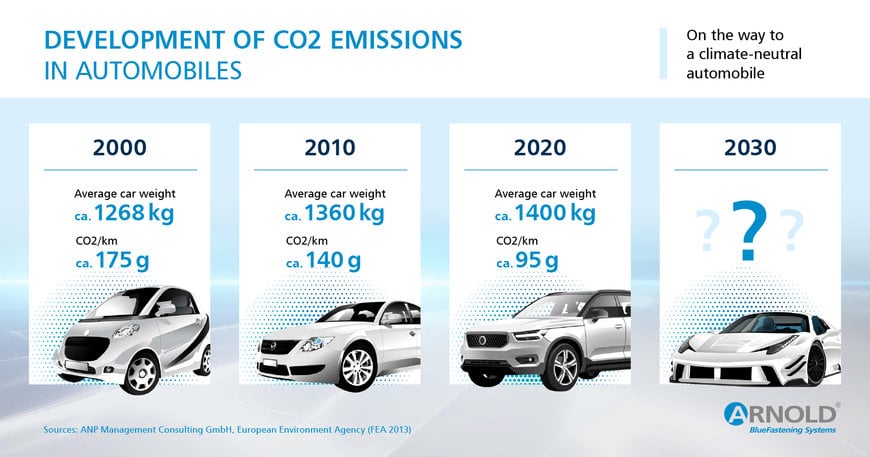
尽管汽车重量不断增加,但欧洲乘用车的二氧化碳排放量必须进一步减少,才能实现气候保护的目标。
借助对燃油消耗的优化以及创新的动力总成概念,现在已经显著减少了二氧化碳的排放量,从 2000 年的 175 g CO2/km 左右到 2010 年的 140 g CO2/km , 2020年降至 95 g CO2/km . 如果要实现未来几年的气候保护目标,这一趋势必须继续下去。
鉴于这种情况,可持续性问题成为德国紧固件制造商 ARNOLD 集团的主要优先事项。除了电动汽车、国际化、轻量化工程和数字化,可持续性是他们确定的五个战略重点之一。
该公司的专家可以通过检查整个价值链并累积所有供应链成员的排放量,从而确定每种产品的具体碳足迹。这意味着供应链下游的公司通过购买他们的产品和服务,就可以将供应商的排放量添加到自己的二氧化碳排放量中,然后将这些排放量传递给他们的客户。
得益于 ACO2-Save 和相关的生产技术变革,德国实现了二氧化碳减排目标,并且其螺钉在生产过程中造成的二氧化碳排放量减少了多达 45%。
ACO2-Save 提供了多种不同的减少二氧化碳排放的方法
在此背景下,Arnold Umformtechnik 推出了 ACO2-Save 计划(这里的 A 代表 Arnold)。 该计划通过以可持续的方式设计和使用紧固件和冷成型零件,为客户减少二氧化碳排放提供更多支持。他们已经在产品开发阶段进行了相应的二氧化碳计算。当客户要求 Arnold 制造零件时,可以使用专门开发的二氧化碳计算器确定产品碳足迹,然后共同进行优化。目标是在开发完成时获得在成本和二氧化碳排放方面实现优化的高质量产品。
设计过程包括以下步骤:通过数字预测工具进行二氧化碳优化工程,对生产或连接技术的改变以及使用创新的连接元件或系统可能带来的二氧化碳优化进行分析。
正是 ACO2 Save 发挥了作用,如下例所示:以前通过传统的机械加工生产一种由铝制的特殊螺钉,其体积为 8,733 mm³,每件重量为 23.58 g。在生产过程中使用了初始体积为 25,630 mm³ 和单件重量为 69.2 g 的车削零件毛坯。经过 ACO² Save 分析后,该零件被转换为 Conform Next 产品系列的成型零件。分析结果是:经过优化,成型坯料的体积仅为 9,135 mm³,每件重量为 24.82 g。除了由于冷成型中使用的材料更少而显著优化成本外,这对特殊螺钉的产品碳足迹也有相当大的影响。